Filling Funnel Product Development - Evolution
- Matt DuBois
- Apr 1, 2021
- 2 min read
Updated: Sep 14, 2021
One example of our Collaboration comes when our customer’s customer has issue with a line that is already in service. In this case a customer had a piece of filling equipment that filled foil pouches with powdered cheese at a very high rate of speed. The platform had 32 funnels that transport the powder from the auger to the collated foil pouches. These funnels were designed originally as fabricated stainless steel parts.

As our customer refined the equipment to increase the speed from what was originally 160 per minute to the current 320 per minute, they were looking for ways to save weight and if possible move away from the approximate $2000 cost of the fabricated stainless funnels. When they approached OMNI we were simply asked to produce a molded direct replacement for the original fabricated funnel. OMNI did some work with the design to maintain the approximate geometry of the stainless funnel. Once the customer saw the design, they loved the cost savings and weight savings they were going to be able to achieve by moving to a molded part. Once the tooling was produced, the parts were sold at a cost that was 95% less and provided a weight savings of 85%. The weight savings allowed them to reach higher speeds and also to extend the life of the chains that drive the funnels by 500%.
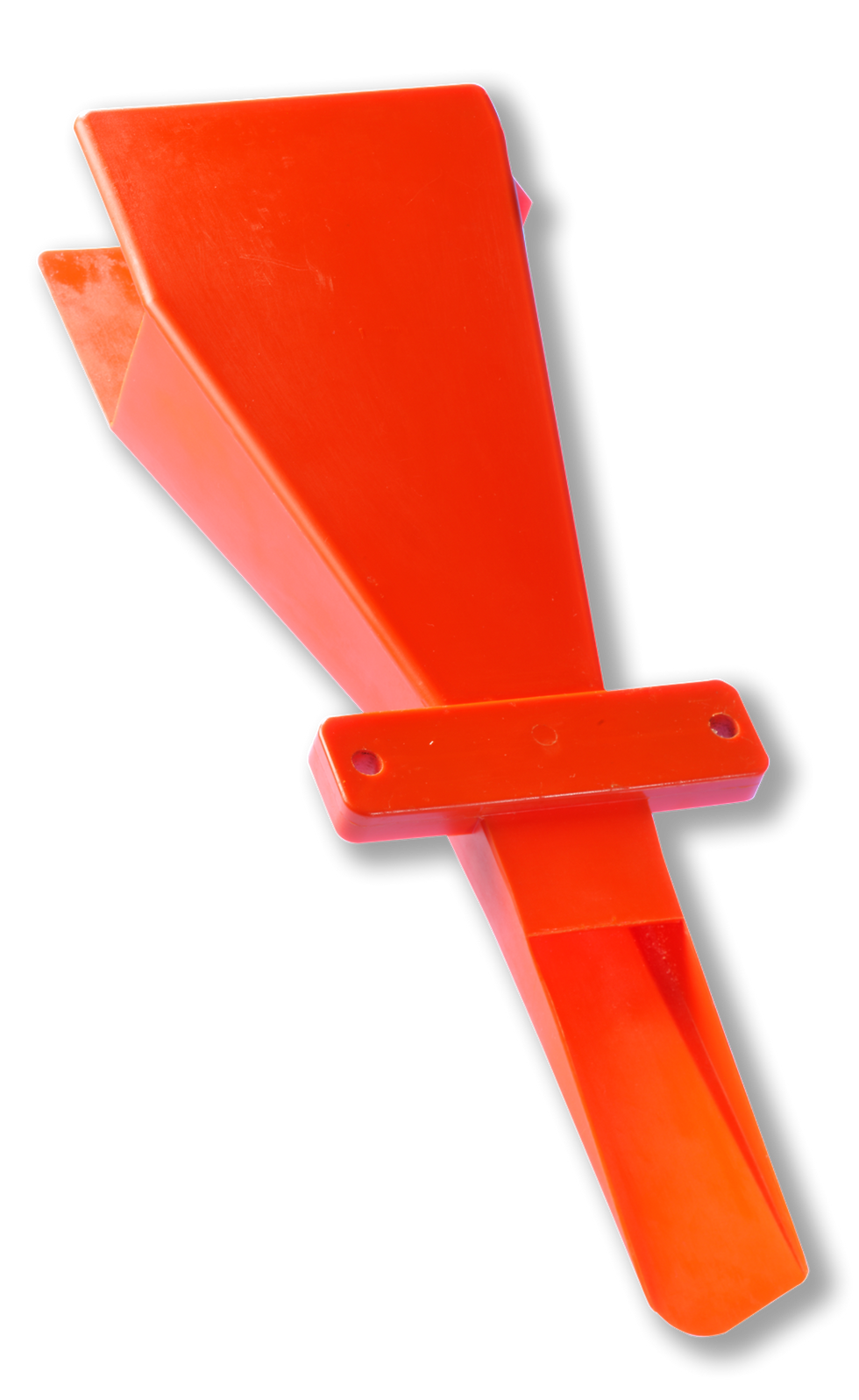
The original stainless funnels were also temperamental and if they were dented or bent the powder would bridge and weights would be inaccurate. This made repairing them was almost impossible. This new molded design eliminated the denting and deformation completely.
After several years of successful running the first version there was a new directive to reduce the wasted powder that missed the funnel at such high speed. The complaint was that the equipment was usually covered with powder. The next revision of the funnel was to design the funnel top to nest with the adjacent funnels to catch as much of the product as possible. The picture of this funnel leaves virtually no gaps for product to fall through. Waste was reduced significantly. With the new changes, some very powerful springs were replaced to hold the duck bill closed and the extremely thin cross section of material (.050”) quickly would get deflected.
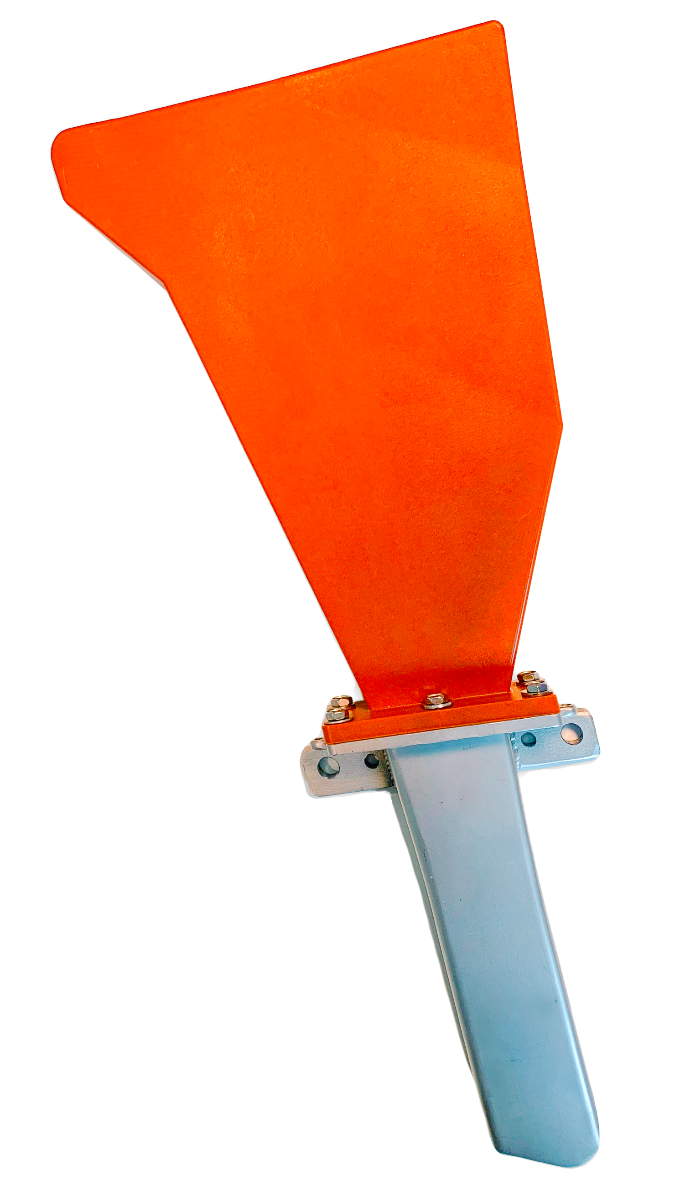
We needed to improve the stability of the duck bill at the bottom of the funnel. We then designed the hybrid version that has a stainless bottom and molded top. The weight savings is still significant and the parts are much more durable. The final revision was made to minimize the static transfer and build up in the funnel top. To do this we use an FDA approved additive “anti-stat” as well as a proprietary additive that not only helps with static but makes the molded funnel top metal detectable.
Comments